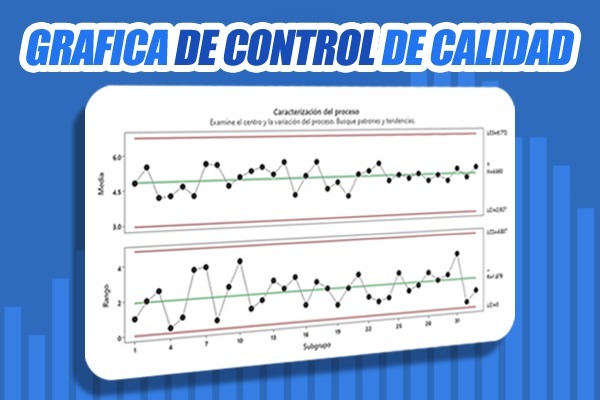
The grafica de control, a pivotal tool in statistical quality control, was developed by Walter A. Shewhart to help organizations better manage their processes. This graphical tool is instrumental in distinguishing between common cause variation random fluctuations inherent to a process and special cause variation variations due to external factors or anomalies.
Control charts track process performance over time, providing a visual representation of data that aids in identifying deviations from expected performance. By plotting data points in relation to control limits, which are set based on statistical calculations, control charts help in discerning whether variations are part of the normal process or indicative of underlying issues.
There are two main types of control charts: variable charts and attribute charts. Variable charts monitor measurable data such as temperature, weight, or time, offering insights into continuous process performance. Attribute charts, on the other hand, focus on countable data, such as the number of defects in a batch of products, highlighting issues in categorical outcomes.
A fundamental concept in control charts is the use of subgroups. These are smaller, manageable clusters of data within a larger dataset. Analyzing subgroups helps in spotting patterns and trends more effectively. By examining variation within and between subgroups, it becomes easier to identify whether the variations are due to random fluctuations or special causes that warrant further investigation.
Interpreting control charts involves several key considerations. Look for patterns such as shifts or trends in the data. Sudden, unexplained changes might signal a special cause of variation. Points that fall outside control limits typically indicate that the process is out of control and needs corrective action. Additionally, observing the general trend whether upward or downward can provide insights into systematic problems affecting the process.
Control charts are invaluable for maintaining and improving process quality. They enable organizations to monitor performance, identify problems, and implement corrective measures to ensure processes remain within desired limits.